Umbrellas are not only a practical necessity but also an excellent canvas for showcasing stunning designs and captivating patterns. When it comes to printing on umbrella fabric, three popular methods stand out: Cylinder Printing, Heat Transfer Printing, and Digital Printing. Each method brings its unique set of advantages and disadvantages. In this blog post, we will explore these printing techniques and how they can elevate the aesthetics of your umbrellas.
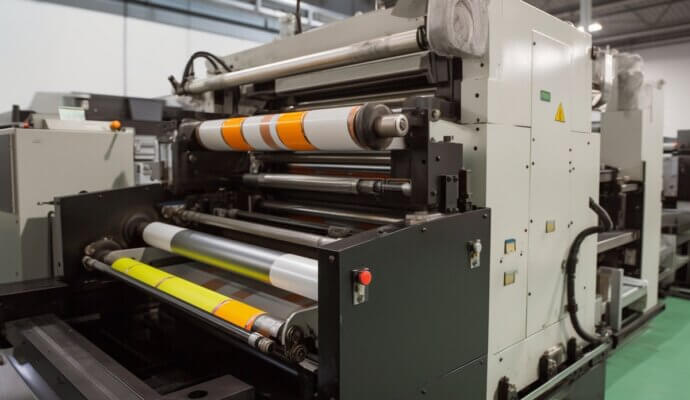
Cylinder printing
Cylinder printing, also known as rotary screen printing, has been used in the umbrella industry to apply designs and patterns onto umbrella fabric. Cylinder printing is a traditional printing method that utilizes cylindrical screens to transfer ink onto the fabric, allowing for high-quality and durable prints. The fabric is fed through the cylinder, and the ink is transferred through the screen, creating intricate designs with vibrant colors.
Here’s how cylinder print is used in the umbrella industry:
- Preparation of the Design: The design or pattern printed on the umbrella fabric is first created digitally or on paper. It is then engraved or etched onto the surface of a cylindrical screen. The engraved areas allow the ink to pass through and be transferred onto the fabric.
- Printing Process: The umbrella fabric is fed through the cylinder printing machine. The cylindrical screen rotates continuously, and as the fabric passes beneath it, the ink is pressed through the engraved areas of the screen onto the fabric. This process is repeated for each color in the design, requiring a separate cylindrical screen for each color.
- Drying and Fixing: After the printing is completed, the fabric may undergo a drying process to fix the ink onto the material, ensuring the design remains vibrant and durable.
Advantages of Cylinder Printing in the Umbrella Industry:
- Durability: Cylinder printing produces long-lasting and durable prints, making it ideal for umbrellas frequently exposed to outdoor elements.
- Color Saturation: The method allows for excellent color saturation, resulting in vibrant and eye-catching designs.
- Efficiency for Large Orders: Cylinder printing is efficient for large production runs, making it cost-effective for bulk orders of umbrellas.
- Consistency: The printing process ensures consistent results across multiple umbrellas, maintaining brand identity and uniformity.
- Versatility: Cylinder printing can accommodate a variety of umbrella fabric types, including polyester, nylon, and other materials commonly used in umbrella manufacturing.
Disadvantages of Cylinder Printing in the Umbrella Industry:
- Long Setup Time: The process of preparing the cylindrical screens can be time-consuming, making it less suitable for on-demand or small-scale production.
- Limited Design Flexibility: Cylinder printing may have limitations when it comes to highly intricate or complex designs, as the process relies on physical screens.
- High Initial Cost: The initial setup and engraving of the cylindrical screens can involve significant costs, which may impact smaller manufacturers or those with limited budgets.
It’s worth noting that advancements in digital printing technology have also made it more accessible and competitive in the umbrella industry. Digital printing offers design flexibility, quicker setup times, and the ability to produce on-demand or personalized prints. As a result, both cylinder printing and digital printing are commonly used in the umbrella industry, catering to different production needs and design requirements.
Except in the umbrella industry, there are several types of cylinder printing methods used in various industries. Each method offers unique advantages and is suitable for specific applications. Here are some of the most common types of cylinder printing:
- Rotogravure Printing: Rotogravure printing, also known as gravure printing, uses a cylindrical plate with recessed cells or wells that hold the ink. The cylinder is engraved with the desired design, and the excess ink is wiped off the surface. As the cylinder rotates, it picks up ink from an ink fountain and transfers it to the substrate. Rotogravure is known for its high-quality and consistent prints, making it suitable for packaging, magazines, and decorative applications.
- Flexographic Printing: Flexographic printing, also called flexo printing, utilizes flexible rubber or polymer plates mounted on a rotating cylinder. The ink is transferred from the plates onto the substrate, typically with the help of a flexible rubber roll called an anilox roll. Flexography is commonly used for printing on corrugated cardboard, labels, flexible packaging, and some types of paper products.
- Letterpress Printing: Letterpress printing involves a cylindrical plate with raised surfaces representing the printing elements. The ink is applied to the raised areas, and the cylinder is pressed directly onto the substrate to transfer the ink. Letterpress was historically popular but is now less commonly used due to the rise of digital printing.
- Intaglio Printing: Intaglio printing is a process that includes several techniques like engraving, etching, and drypoint. In this method, the design is incised or etched into the surface of a metal cylinder. The cylinder is then inked, and the excess ink is wiped off, leaving ink only in the recessed areas. The substrate is pressed against the cylinder, and the ink is transferred to the substrate. Intaglio printing is used for producing banknotes, stamps, and fine art prints.
- Screen Printing: While not exclusively cylinder printing, screen printing can involve a cylindrical screen for continuous printing. A cylindrical screen is wrapped around a rotating drum, and ink is forced through the screen onto the substrate below. Screen printing is versatile and can be used on a wide range of materials, including fabrics, glass, metal, and plastics.
These cylinder printing methods differ in their application, complexity, and the types of substrates they can print on. Each method has its strengths and is selected based on the specific requirements of the printing job.
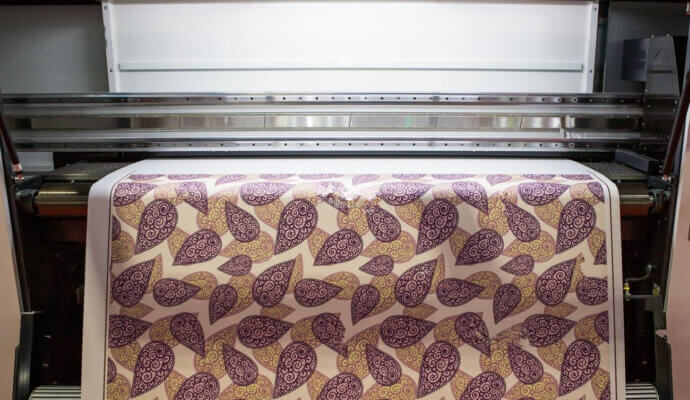
Heat Transfer Printing
Heat transfer printing is commonly used in the umbrella industry to apply designs and graphics onto umbrella fabric. Heat transfer printing is a versatile method that involves transferring designs from a special paper or vinyl onto the umbrella fabric using heat and pressure. The design is first printed onto the transfer medium, and then it’s bonded to the fabric through a heat press.
Here’s how heat transfer printing is utilized in the umbrella industry:
- Design Preparation: The design or pattern to be printed on the umbrella fabric is first created digitally or on paper. The design is then printed onto a special heat transfer paper or vinyl using an inkjet or laser printer.
- Transfer Process: The heat transfer paper or vinyl is placed on the umbrella fabric, and heat and pressure are applied using a heat press machine. The heat and pressure activate the ink on the transfer medium, causing it to transfer and adhere to the fabric.
- Peeling and Cooling: After the transfer process, the heat transfer paper or vinyl is carefully peeled off, leaving the printed design on the umbrella fabric. The fabric is allowed to cool, ensuring that the design adheres securely.
Advantages of Heat Transfer Printing in the Umbrella Industry:
- Photorealistic Prints: Heat transfer printing allows for high-quality, photorealistic images with fine details and shading. This makes it suitable for reproducing complex designs and realistic artwork on umbrellas.
- Design Customization: Heat transfer printing enables customization and variable data printing, making each umbrella unique. This is ideal for creating personalized or branded umbrellas for promotional purposes.
- Quick Turnaround: Heat transfer printing has a shorter setup time compared to some other printing methods, making it suitable for on-demand or small-scale production.
- Cost-Effective for Short Runs: Heat transfer printing is cost-effective for producing smaller quantities of printed umbrellas, making it suitable for limited editions or personalized orders.
- No Color Limitations: Heat transfer printing allows for a wide color gamut, offering vibrant and vivid colors on the umbrella fabric.
Challenges of Heat Transfer Printing in the Umbrella Industry:
- Limited Durability: While heat transfer prints can be durable, they may not be as long-lasting as some other printing methods, especially for umbrellas frequently exposed to harsh weather conditions.
- Possibility of Peeling or Fading: Over time, the transferred design may peel or fade, especially if exposed to rough handling or extreme weather.
- Print Texture: Some heat transfer prints may have a slight texture on the fabric surface due to the adhesive used in the transfer process. This may not be ideal for certain designs or applications that require a smooth surface.
Despite these challenges, heat transfer printing remains a popular choice in the umbrella industry, especially for short-run or custom orders. Manufacturers can utilize heat transfer printing to produce eye-catching and personalized umbrella designs for various markets and promotional purposes. Proper selection of transfer materials and post-print treatment can enhance the durability and longevity of heat transfer prints on umbrellas.
There are several types of heat transfer printing methods, each with its unique characteristics and applications. Heat transfer printing is a versatile process used to transfer designs, patterns, or images onto various substrates, such as fabric, ceramic, metal, or paper, using heat and pressure. Here are some common types of heat transfer printing:
- Heat Transfer Paper Printing: In this method, an image is printed onto a special heat transfer paper using an inkjet or laser printer. The printed paper is then placed on the substrate, and heat is applied using a heat press machine. The heat activates the ink on the paper, causing it to transfer and adhere to the substrate.
- Sublimation Printing: Sublimation printing uses special ink that, when heated, transforms from a solid to a gas without going through the liquid stage. The gas infuses into the substrate’s surface, creating a permanent, full-color image. Sublimation is commonly used for printing on polyester fabrics, mugs, and other coated materials.
- Vinyl Heat Transfer Printing: This method involves cutting a design or lettering from colored vinyl using a computer-controlled cutter. The vinyl is then heat-pressed onto the substrate, and the excess material is removed, leaving the desired design adhered to the surface.
- Plastisol Transfers: Plastisol transfers involve printing a design on a special release paper with plastisol ink. The transfer is then heat pressed onto the substrate, and the ink adheres to the material. Plastisol transfers are commonly used for apparel and promotional products.
- Heat Transfer Vinyl (HTV) Printing: Similar to vinyl heat transfer, HTV involves cutting designs from colored vinyl sheets and heat pressing them onto fabrics, creating custom apparel.
- Digital Heat Transfer Printing: This method combines digital printing technology with heat transfer processes. The design is printed onto heat transfer paper using an inkjet or laser printer, and then the image is transferred to the substrate using a heat press.
- Hot Stamping: While not strictly a heat transfer printing method, hot stamping involves applying colored or metallic foils to a substrate using heat and pressure. This method is commonly used for printing on paper, cardboard, and certain plastics.
Each heat transfer printing method has its advantages and is suitable for different types of substrates and applications. Manufacturers and designers choose the appropriate heat transfer method based on factors like the material being printed, the complexity of the design, the desired durability, and the quantity of items to be produced.
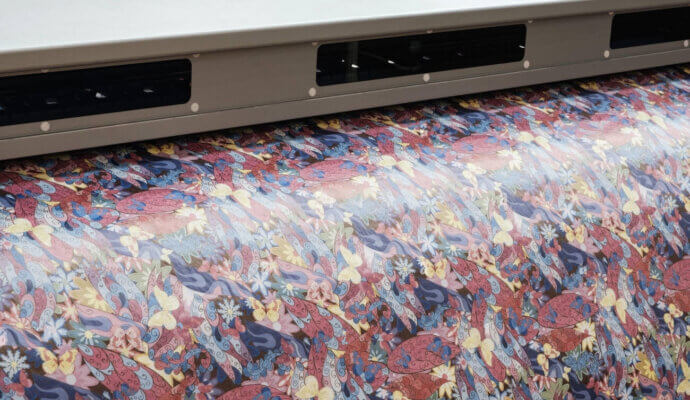
Digital Printing
Digital printing is a modern method that involves printing directly onto the umbrella fabric using inkjet or laser technology, replicating the design from a digital file. It has become increasingly prevalent in the umbrella manufacturing sector due to its versatility, design flexibility, and high-quality output. This method allows manufacturers to print directly onto umbrella fabric from digital files, eliminating the need for traditional printing plates and offering numerous advantages.
Here are some key aspects of digital print in the umbrella industry:
- Design Flexibility: Digital printing allows for a wide range of design possibilities, including intricate patterns, photorealistic images, and vibrant colors. Designers can create custom prints with ease, enabling personalized and unique umbrella designs.
- Direct Printing: Digital printing allows printing directly from digital files, such as computer graphics or images from digital cameras. This eliminates the need for physical plates, which reduces setup time and costs.
- On-Demand Printing: Digital printing enables on-demand production, meaning umbrellas can be printed in smaller quantities as needed. This reduces inventory costs and waste, making it an economical choice for small or niche markets.
- Variable Data Printing: Digital printing technology allows for variable data printing, which means each umbrella can have unique information, such as names, different graphics, or customized messages. This is particularly useful for promotional or personalized umbrella campaigns.
- High Print Quality: Digital printing provides excellent print quality, capturing intricate details and producing smooth color gradients. This is especially important for complex designs or artwork that require precise reproduction.
- Quick Turnaround: Digital printing has a shorter setup time compared to traditional methods like cylinder printing. This enables faster production and delivery times, making it suitable for time-sensitive projects and fast-paced markets.
- Environmentally Friendly: Many digital printing technologies use water-based or eco-solvent inks, which are more environmentally friendly compared to some traditional printing methods that use solvent-based inks.
- Suitable for Short Runs: Digital printing is cost-effective for short to medium print runs due to there being no plate-making expenses, making it ideal for smaller umbrella manufacturers or those producing limited editions compared to traditional printing methods.
- Versatility: Digital printing can handle various umbrella fabric types, including polyester, nylon, pongee, and other materials commonly used in umbrella manufacturing.
Challenges of Digital Printing in the Umbrella Industry:
- Durability: While digital printing produces high-quality prints, the durability of the printed design may not be as robust as some traditional printing methods like cylinder printing, especially for umbrellas exposed to harsh weather conditions.
- Limited Special Effects: Digital printing may have limitations in achieving certain special effects like metallic finishes or embossing, which traditional printing methods can handle.
- Cost for Large Orders: Digital printing might be more expensive for large production runs compared to cylinder printing.
Despite these challenges, the numerous advantages of digital printing, including design flexibility, cost-effectiveness for short runs, and on-demand capabilities, make it a popular and viable choice for the umbrella industry. Manufacturers can leverage digital printing technology to produce eye-catching, personalized, and high-quality umbrellas that cater to various markets and customer preferences. As technology continues to advance, digital printing is expected to play an even more significant role in the umbrella manufacturing process.
There are several types of digital printing methods, each with its unique characteristics and applications. Here are some common types of digital printing methods:
- Inkjet Printing: Inkjet printing is one of the most widely used digital printing methods. It involves propelling tiny droplets of ink onto the substrate to create the desired image. Inkjet printers are available in various sizes, from desktop printers for small-scale printing to large-format printers for wide-format applications.
- Laser Printing: Laser printing uses a laser beam to create an electrostatic image on a photosensitive drum or belt. The charged toner particles are then transferred and fused onto the substrate using heat. Laser printers are commonly used for high-speed, high-quality printing, particularly in office environments.
- Dye Sublimation Printing: Dye sublimation printing is commonly used for printing on fabrics, apparel, and rigid materials like ceramics and metals. It involves using heat to transfer dye onto the substrate, where the dye turns into a gas and infuses into the material’s surface, creating a permanent image.
- Electrophotographic Printing (Electrostatic Printing): Electrophotographic printing, also known as electrophotography or xerography, is the technology used in laser printers and photocopiers. It involves creating an electrostatic image on a photosensitive surface and then transferring toner particles to the substrate using electrostatic attraction.
- Direct-to-Garment (DTG) Printing: DTG printing is a digital printing method specifically designed for printing on textiles and garments. It uses specialized inkjet technology to print designs directly onto the fabric, allowing for vibrant and detailed prints on apparel.
- UV Printing: UV printing uses UV-curable inks that dry instantly when exposed to UV light. It can print on a wide range of substrates, including rigid materials like glass, acrylic, wood, and metal.
- Solvent Printing: Solvent printing uses solvent-based inks that can be applied to a variety of materials, including vinyl, banners, and adhesive-backed materials. These inks are weather-resistant and durable, making them suitable for outdoor applications.
- Latex Printing: Latex printing uses water-based latex inks that offer environmental advantages compared to solvent inks. This method is suitable for printing on a variety of media, including textiles, banners, and self-adhesive materials.
Please note that digital printing technology is continuously evolving, and new methods and advancements may have emerged since my last update. Manufacturers and designers choose the appropriate digital printing method based on factors such as the substrate, desired print quality, durability requirements, and scale of production.
Summary
Each printing method – Cylinder Printing, Heat Transfer Printing, and Digital Printing – has its strengths and weaknesses. Cylinder printing excels in color saturation and durability, making it a great choice for large-scale productions. Heat transfer printing allows for photorealistic images and customization, ideal for smaller orders. Digital printing offers high-quality prints, on-demand capabilities, and design flexibility, but may be more cost-effective for smaller runs.
When choosing the right printing method for your umbrella manufacturing, consider your budget, order quantity, and the level of design intricacy required. With the right printing technique, your umbrellas will become a stunning canvas, showcasing your creativity to the world.
2 thoughts on “Blog”
Can the way an umbrella is packaged really make a significant impact on the success of a brand? How can innovative packaging strategies differentiate a brand in a competitive market?
Yes, the way an umbrella is packaged can certainly elevate the brand and make it stand out. There are many different methods of packaging, and the approach you choose depends on how you want to convey the brand’s identity and values. For example, sleek and minimalist packaging could communicate a modern, high-end feel, while eco-friendly packaging might appeal to environmentally conscious consumers. Ultimately, packaging is a powerful tool to express the brand’s story, make a memorable impression, and create a unique customer experience.